Have you seen this acronym floating around, SCM software, and have you wondered what it means and how it can help improve my productivity and profitability?
To answer that question, you've hit the right article. In this article, we'll be looking at the best supply chain management software. We'll compare the top 5 supply chain management software currently available on the market and examine the features, pros, and cons of each one. By the end of this article, you will be familiar with SCM software and its uses and have found your favourite one.
>> Read more: Logistics App Development Guide: Features, Tech Stack, & Use Cases
What is Supply Chain Management Software?
Supply chain management (SCM) software refers to a category of software applications designed to support and optimize various activities and processes within the supply chain. It provides companies with tools and functionalities to effectively plan, execute, monitor, and control their supply chain operations.
Features of Supply Chain Management Software
Supply chain management software typically encompasses a range of modules or features that address specific areas of the supply chain. Some standard functionalities of SCM software include:
Demand Planning and Forecasting: SCM software helps companies analyze historical data, market trends, and other factors to forecast customer demand accurately. It assists in creating demand plans, managing seasonality, and aligning production and procurement activities accordingly.
Inventory Management: SCM or free inventory management software enables companies to track inventory levels, locations, and movements across the supply chain. It provides real-time visibility into stock availability, automates inventory replenishment, optimizes order quantities, and reduces carrying costs.
Procurement and Supplier Management: SCM software streamlines the procurement process, from requisition to purchase order creation and supplier management. It helps manage supplier relationships, track supplier performance, streamline supplier onboarding, and ensure compliance with purchasing policies.
Warehouse Management: SCM software optimizes warehouse operations by automating tasks such as receiving, put-away, picking, packing, and shipping. It provides visibility into inventory levels, improves order accuracy, and enhances warehouse efficiency through better resource allocation and process optimization.
Transportation Management: SCM software facilitates efficient management of transportation activities, including carrier selection, route optimization, load planning, and shipment tracking. It helps companies reduce freight costs, optimize delivery schedules, and enhance logistics efficiency.
Supply Chain Visibility and Analytics: SCM software provides real-time visibility into supply chain activities, allowing companies to monitor and track key performance indicators (KPIs) and metrics. It enables data-driven decision-making, identifies bottlenecks or inefficiencies, and supports continuous improvement initiatives.
Demand-Supply Balancing: SCM software helps companies achieve optimal alignment between demand and supply through better synchronization of production, procurement, and distribution activities. It enables companies to respond quickly to changes in customer demand, minimize stockouts or excess inventory, and improve overall supply chain responsiveness.
Collaboration and Communication: SCM software facilitates collaboration and information sharing among supply chain stakeholders, including suppliers, manufacturers, distributors, and retailers. It enables real-time communication, document sharing, and collaborative planning, enhancing coordination and reducing lead times.
Supply chain management software aims to optimize supply chain processes, reduce costs, enhance operational efficiency, improve customer service, and drive overall supply chain performance. It provides companies the tools and capabilities to streamline their supply chain operations, adapt to changing market dynamics, and gain a competitive advantage in today's global business environment.
>> Read more: Top 10 Innovative Mobile Applications for Logistics Companies
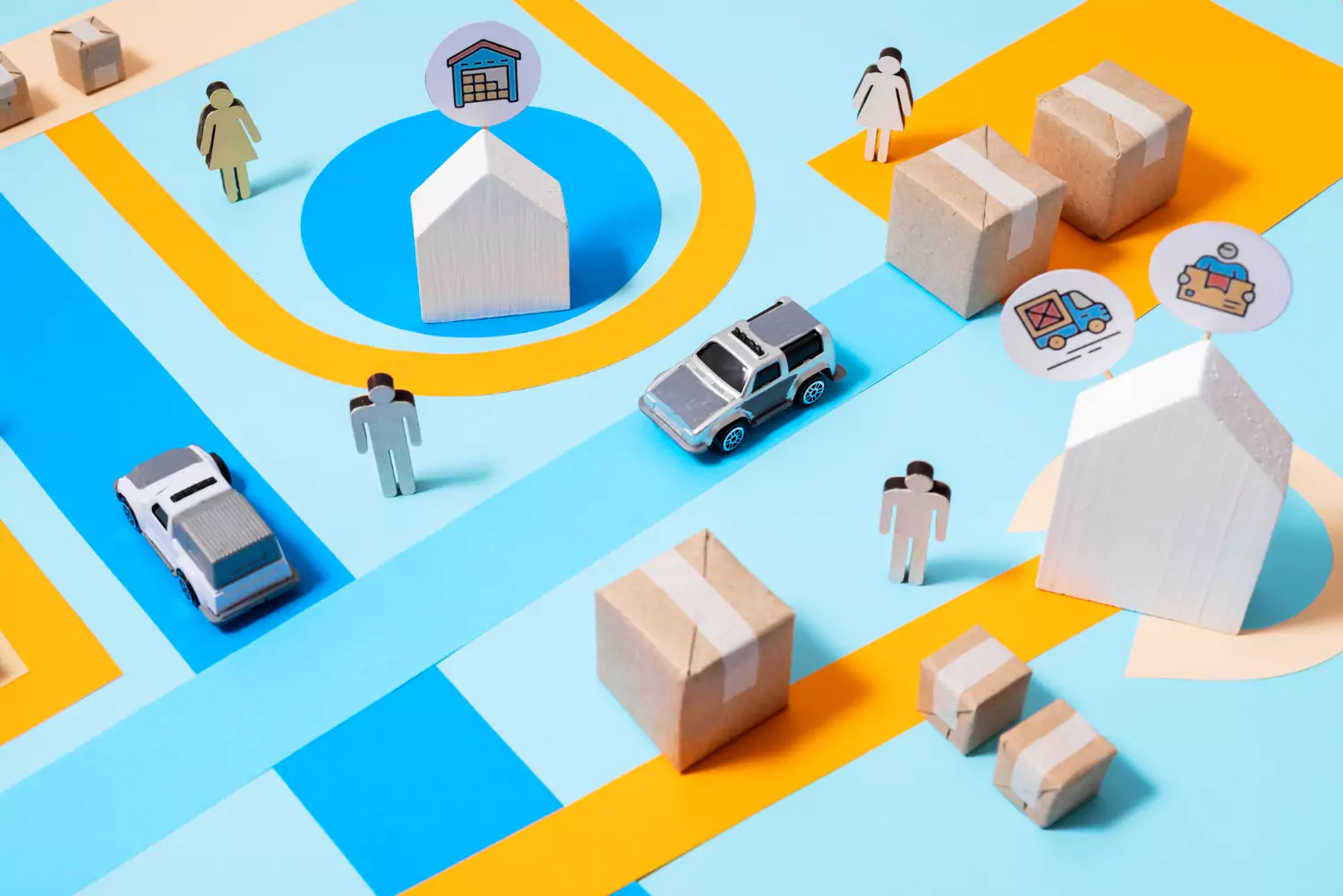
SCM Components
SCM Component 1: Planning
The first part of any supply chain process is the planning stage. SCM planning is where you determine your requirements, your materials, labour and money allocations, and your overall budget. Here is the stage for laying out schedules, timeframes, milestones, and goals. Proper supply chain planning reduces waste and problems throughout the development lifecycle.
SCM Component 2: Sourcing
The sourcing stage of supply chain management follows the planning stage. In this component, you now see where you will source everything you need to execute the supply chain project. You will deal with suppliers and other procurement tasks, hoping everything fits within your budget and can be sourced on time.
SCM Component 3: Execution
Supply chain execution is where you go ahead and begin the project, start making the product, or perfect the service you will eventually bring to customers and the market. It is the production stage, and if you've done your SCM planning and SCM sourcing correctly with great software, it should proceed as streamlined as possible.
SCM Component 4: Delivery
After the production phase or execution stage of SCM, it is time to deliver the goods. Here is where you present the product to the client, market or stakeholders. In this stage, you will deal with shipping and distribution logistics, vital tools within any SCM solution. This would be the final stage unless there are problems, so move on to component number 5.
SCM Component 5: Returns
Sometimes, when the market, stakeholder, or client receives a product that has undergone the supply chain process, there is a problem or an issue that needs to be fixed. The returning component of SCM prepares you to deal with these returns. You can easily track what is coming back and what needs to be resolved and offer assurances to the customer that you are committed to staying on top of the issue.
Models of Supply Chain Management
Push Model
In the push model, companies forecast customer demand based on historical data, market trends, and other factors. They then manufacture or procure products based on these forecasts and push them into the supply chain. This model is suitable for industries with stable demand patterns and longer production lead times.
Pull Model
The pull model operates in response to actual customer demand. Products are produced or procured only when there is a confirmed order or customer demand signal. This model minimizes the risk of excess inventory and focuses on achieving a more responsive and customer-driven supply chain.
Lean Model
The lean model aims to minimize waste and optimize efficiency throughout the supply chain. It focuses on reducing inventory, eliminating non-value-added activities, and achieving just-in-time (JIT) production and delivery. The lean model emphasizes continuous improvement and the elimination of process bottlenecks.
Agile Model
The agile model emphasizes flexibility and responsiveness to rapidly changing market dynamics and customer demands. It involves maintaining a flexible supply chain that can quickly adapt to changes in customer preferences, market trends, and supply disruptions. Collaboration and real-time information sharing with suppliers and partners are critical in the agile model.
>> Read more: Top Agile Frameworks In Software Engineering 2023
Efficient Consumer Response (ECR)
ECR is a model focused on improving the overall efficiency of the supply chain in the retail industry. It involves collaboration between retailers, manufacturers, and distributors to optimize inventory management, reduce lead times, and enhance product availability. ECR aims to achieve cost reduction, improved customer service, and streamlined operations.
Vendor-Managed Inventory (VMI)
In the VMI model, the responsibility for managing inventory rests with the supplier rather than the customer. The supplier monitors the inventory levels at the customer's location and ensures timely replenishment based on predefined agreements. VMI can improve inventory visibility, reduce stockouts, and enhance supply chain efficiency.
Just-in-Time (JIT) Model
The JIT model focuses on minimizing inventory levels and carrying costs by synchronizing production and delivery to customer demand. It involves precise coordination between suppliers, manufacturers, and distributors to ensure that materials and products arrive at the right place, in the right quantity, and at the right time.
Outsourcing Model
The outsourcing model involves partnering with external suppliers or service providers to perform certain supply chain activities. Organizations outsource functions such as manufacturing, warehousing, transportation, or IT services to leverage specialized expertise, reduce costs, and focus on core competencies.
Green/Sustainable Model
The green or sustainable supply chain model emphasizes environmentally friendly practices throughout the supply chain. It focuses on reducing carbon emissions, minimizing waste generation, optimizing energy consumption, and selecting eco-friendly suppliers. The sustainable model integrates environmental considerations into supply chain decision-making.
Digital/Technology-Driven Model
With the advent of digital technologies, the supply chain management landscape has evolved. This model incorporates technologies such as automation, Internet of Things (IoT), artificial intelligence (AI), blockchain, and data analytics to enhance supply chain visibility, improve forecasting accuracy, enable real-time decision-making, and drive operational efficiency.
>> Read more:
What Are The Different Types Of Supply Chain Management Software?
Several examples of supply chain management systems exist, some more specialized and others more general. Here are some of the prominent examples of SCM and what purposes these can fulfil:
Enterprise Resource Planning (ERP) Systems
ERP systems integrate various business functions into a centralized platform, including supply chain management. They provide end-to-end visibility and control over the entire supply chain, encompassing inventory management, procurement, production planning, and logistics.
Warehouse Management Systems (WMS)
WMS software optimizes warehouse operations and inventory management. It includes inventory tracking, order fulfilment, labour management, optimization of slotting, and warehouse layout. WMS software helps improve warehouse efficiency, accuracy, and inventory visibility.
Transportation Management Systems (TMS)
TMS software helps companies optimize transportation planning, execution, and freight management. It handles functions like carrier selection, routing and scheduling, load planning, shipment tracking, freight auditing, and reporting. TMS software enhances logistics efficiency, reduces transportation costs, and improves customer service.
Demand Planning and Forecasting Software
Demand planning and forecasting software utilize historical data, statistical models, and predictive analytics to forecast customer demand accurately. It helps companies optimize inventory levels, production planning, and procurement decisions, minimizing stockouts and excess inventory.
Inventory Management Systems
Inventory management software tracks and manages inventory levels, locations, and movements in real time. It includes stock tracking, order fulfilment, replenishment planning, demand analysis, and stock optimization. Inventory management systems help optimize inventory levels, reduce carrying costs, and improve order fulfilment.
Supplier Relationship Management (SRM) Systems
SRM software focuses on managing supplier relationships and collaboration. It includes features like supplier evaluation, performance monitoring, contract management, and collaboration tools. CRM software helps optimize supplier selection, improve supplier performance, and ensure compliance with supplier contracts.
Procurement Systems
Procurement software streamlines the procurement process, from requisition to purchase order creation and supplier management. It includes features like supplier catalogue management, purchase order automation, contract management, and spend analysis. Procurement systems help automate and optimize procurement activities, ensuring timely and cost-effective purchasing.
Supply Chain Analytics and Business Intelligence
Supply chain analytics and business intelligence software provide insights and performance metrics based on supply chain data. They include features like data visualization, dashboards, reporting, and advanced analytics. These tools help identify trends, optimize supply chain processes, and support data-driven decision-making.
Collaborative Planning, Forecasting, and Replenishment (CPFR) Systems
CPFR software enables collaboration between trading partners, including manufacturers, suppliers, and retailers. It supports joint demand planning, forecasting, and inventory replenishment, facilitating efficient supply chain coordination and reducing stockouts and excess inventory.
Order Management Systems (OMS)
OMS software focuses on managing and processing customer orders efficiently. It includes features like order capture, fulfilment, tracking, and customer communication. OMS software helps streamline the order-to-cash process and improves order accuracy and customer satisfaction.
It's important to note that some SCM software solutions may incorporate multiple functionalities, combining features from different types of software. The specific software requirements will depend on the company's supply chain structure, industry, and specific needs.
>> Read more: The Role Of On-Demand Delivery In The Market
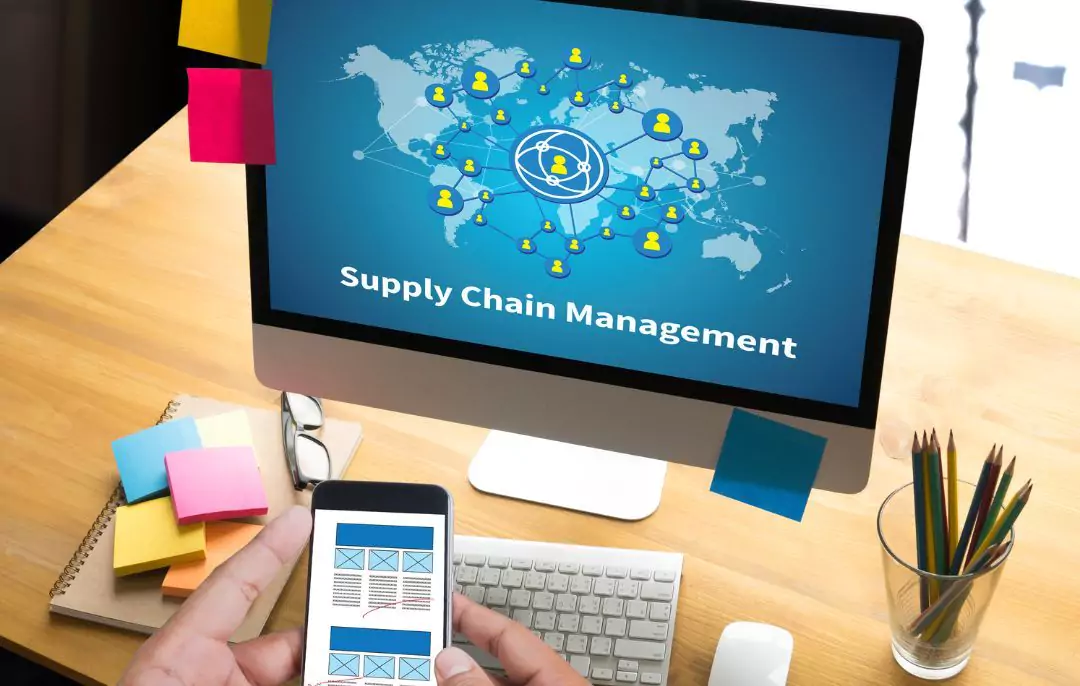
6 Leading Supply Chain Management Software
Are you ready for this rundown of the top supply chain planning tools? We hope so. Everything you want to know about SCM and its features and functionalities will be laid out in the following reviews, from household names like Microsoft, Oracle and SAP to niche brands like Logility and Infor. Here we go with the list of supply chain management software:
SAP Supply Chain Management Software
SAP is a mammoth software development corporation originally from Germany, with operations worldwide. They make ERP, SCM, financial management, accounting, and more.
SAP has many products for supply chain management. These include:
- Supply chain planning products like:
- SAP Integrated Business Planning for Supply Chain,
- SAP Ariba Supply Chain Collaboration for Buyers.
- Supply chains logistics tools like:
- SAP Extended Warehouse Management,
- SAP Transportation Management.
- Product lifecycle management tools like:
- SAP Product Lifecycle Costing,
- SAP Portfolio and Project Management,
- SAP Enterprise Product Development,
- SAP S/4HANA Cloud for projects, project collaboration.
Pros:
Hands down, SAP makes some of the best supply chain management software. The vast ecosystem of SCM and SCM-related products are great for companies to pick and choose suitable SCM modules. SAP products work well with IoT devices, or the Internet of Things, an automated data-generating and sharing system that streamlines many of your operations and gives added supply chain visibility.
Cons:
The first drawback is that, while SAP prices are not listed, this is supposedly on the pricier end of the SCM cost scale. Also, some people prefer to avoid having to choose from their wide ecosystem of SCM products. SAP could be more user-friendly when onboarding and learning the tools. However, most people get the hang of it.
Pricing:
Contact SAP for the prices of all their SCM products.
Microsoft Dynamics 365 Supply Chain Management
Everyone knows Microsoft for Outlook, Word, Excel, Office, and Zoom. But Microsoft also makes a top supply management software solution. It's part of the Microsoft Dynamics 365 package.
You can leverage MS Dynamics 365 to plan an entire product lifecycle from the project start until the end of supply chain protocols.
You have your standard demand forecasting that is also useful for planning. As for procurement management, Dynamics helps with vendor communication and collaboration. You also get a bunch of standard inventory management and warehouse management tools.
Pros:
Microsoft 365 users of SCM tools will probably love doing product lifecycle planning with this app. Maintaining a high level of finished product quality is a huge benefit.
There is solid resource allocation planning to make sure inventories and warehousing remain optimized for any project or unforeseeable task. You get all sorts of useful features like barcodes and QR codes.
Microsoft gets points for relative ease of use and for displaying clear pricing information on their site. Moreover, the Dynamics API allows for more inter-functionality between Microsoft's CRM and ERP, including SCM.
Cons:
The Microsoft Corporation naturally turns off some users. For this reason, they won't be running to subscribe to Dynamics 365 for SCM, ERP or other business processes.
Pricing:
Microsoft Dynamics 365 Supply Chain Management costs $1980 per user per month.
Logility
Logility may be a more minor brand name than SAP or Microsoft. Still, in the SCM world, Logility is quite a meaningful name. Logility is famous for using loads of artificial intelligence in its SCM features.
For four product life cycle tasks, Logility has total lifecycle planning, traceability tools, and merchandise and assortment planning. There is your standard inventory optimization and supply and manufacturing planning and optimization.
Logility has many tools for supply data analytics like IoT. Finally, this is one excellent supply chain management cloud software for demand forecasting.
Pros:
Beginning with Logiltiy's demand module, you get planning and demand to sense, a highly tuned forecaster. There is also causal forecasting and proportional profile planning for better forecasts. Manufacturing SCM tasks benefit from multi-step routing and post-production routing automations which reduce possible errors and speed up production.
The IoT, AI, automation, and workflows make Logility a highly streamlined user experience. Logility also scores points for having well-designed dashboards and interfaces.
Cons:
Logility is more useful at large companies and enterprise-level size operations. There may be better choices if you are running a small business or startup.
Pricing:
Contact Logility for pricing.
>> Read more: Top 5 Marine Management Software in 2023
Oracle NetSuite ERP Supply Chain Management
Regarding shopping around for the best supply chain planning tool, you could only do a little better with Oracle NetSuite ERP.
Oracle, like SAP, is a humongous software company, making all sorts of business applications for accounting, CRM, professional services, infrastructure management and HR. Their ERP SCM module is helpful for many industries like healthcare, energy, financial services, manufacturing and retail. As for SCM tools, you get supply planning and a wider supply chain execution suite.
Pros:
Supply planning is one area that Oracle NetSuite excels at. You get solid demand forecasting and analysis, inventory stock replenishment management, and purchase orders.
Everything in your NetSuite system stays up-to-date in real-time with automated syncing and other supply planning functionality, thanks to tech like IoT.
Oracle NetSuite ERP Supply Chain Management has advanced features for further SCM optimization, like stakeholder engagement, scheduling and budgeting.
Cons:
Again, no listed prices, and from other reports, you'll need a decent budget to run this software for your supply chain purposes.
Some onboarding time will be required, as this will feel less user-friendly right out of the box.
Pricing:
Contact Oracle for NetSuite ERP prices.
Infor Supply Chain Management
Infor is an enterprise resource planning software maker which includes excellent SCM functionality. Infor's many OSCM software packages are perfect for the automotive industry and other industrial manufacturing businesses.
Infor is also the umbrella brand name for many products: SCM, WMS, human capital management or HCM, financials and supply management, Nexus supply chain finance, Infor supply planning, and Nexus supply management. Here we'll talk about the basic SCM.
Pros:
Infor knows how to tailor its ERP and SCM tools to specific industries in heavy manufacturing or the servicer sector. As mentioned, this is a top SCM tool for the automotive industry. The SCM module is end-to-end, covering all the steps of supply chains, from planning to execution to deliveries and even returns.
Everything is cloud-based, and all the valuable data gets turned into actionable business intelligence delivered on fine Info reports.
Cons:
While Infor covers many business types, it may be ideal for manufacturing and less for small businesses in the service sector, like boutique agencies, ecommerce or self-employed people. No listed prices on their website, and likely a bit of an expensive set of SCM and ERP tools.
Pricing:
Visit Infor's website to request pricing info.
E2open
E2open may not be a household name in the business SaaS world. Still, when it comes to the best transportation management SCM, this is a solid choice. The company has its HQ in Auston but offices globally.
E2open is a data-driven supply chain optimization software solution. It specializes in SCM risk management, ESG solutions for supply chains (environmental, social and governance), control tower operations for optimized end-to-end supply chains, procurement, logistics and AI.
Pros:
E2open has many packages, so let's begin with straight-up SCM. You got your purchase orders, supply forecasting, SCM collaboration, and buy-sell management tools.
There is also great invoicing, product costing, risk and quality control, and product lifecycle management.
There is demand planning and demand sensing, multi-echelon inventory management, allocation maximization, and operations and distribution planning management for supply planning. Once again, huge benefits for TMS business needs with E2open.
Cons:
E2open is not your SCM system if you are a startup or small business. The costs are not competitive, and the functionalities might be more than a small operation needs.
This SaaS has quite the dry look and feels to its design, which isn't awful, but some might prefer something with more excellent aesthetics.
Pricing:
Contact E2open for pricing information.
In conclusion
And so we wrap up this review of the best supply chain management solutions. Which one is truly the best for your business needs? You may agree that SAP makes the best SCM tool, or you like one of the lesser-known names like Logility.
Either way, any of these supply management solutions will optimize your business processes and streamline the work at every phase of the product or project lifecycle, ultimately making your workplace more efficient and considerably boosting your potential profitability.
>>> Follow and Contact Relia Software for more information!
- Designing an application
- development