In the past, companies relied heavily on manual labor, paper, and machinery to keep the product development procedure moving. The system worked for a long time, but it was often slow, expensive, and hard to change when needs changed.
Today, new technology helps manufacturers make better choices, work faster, and link their systems in smarter ways. This is called digital transformation, and many real-world digital transformation examples in manufacturing show how it helps improve speed, quality, and flexibility.
In this article, we'll describe digital transformation in manufacturing, why it's important, and how organizations can use it to enhance quality, minimize waste, and meet customer expectations. We will also include actual case studies, typical difficulties, and possible future advancements.
>> Read more:
- The Importance Of Digital Transformation in Healthcare
- Digital Transformation in Banking and Financial Services
- How is Digital Transformation Changing The Real Estate Industry?
What Is Digital Transformation in Manufacturing?
Digital transformation in manufacturing means using digital technologies like cloud software, IoT, AI, and automation to improve the operation of manufacturers. The main goals are to keep up with what consumers want, make better choices, and cut down on waste. Digital tools change how things are planned, manufactured, tracked, and improved, not just adding more computers or equipment in the developing process.
For instance, a business could set up machine sensors to gather real-time data. This lets the team know whether something is ready to break so they can fix it before it causes delays. Or, they could use computer software to plan out goods before they are built to visualize what the product will look like in reality from the initial idea.
What’s more, manufacturing businesses can use a heavy equipment maintenance app to schedule timely repairs and track machinery health, reducing downtime and extending equipment lifespan. These developments enable manufacturers to save money, operate more quickly, and produce better goods.
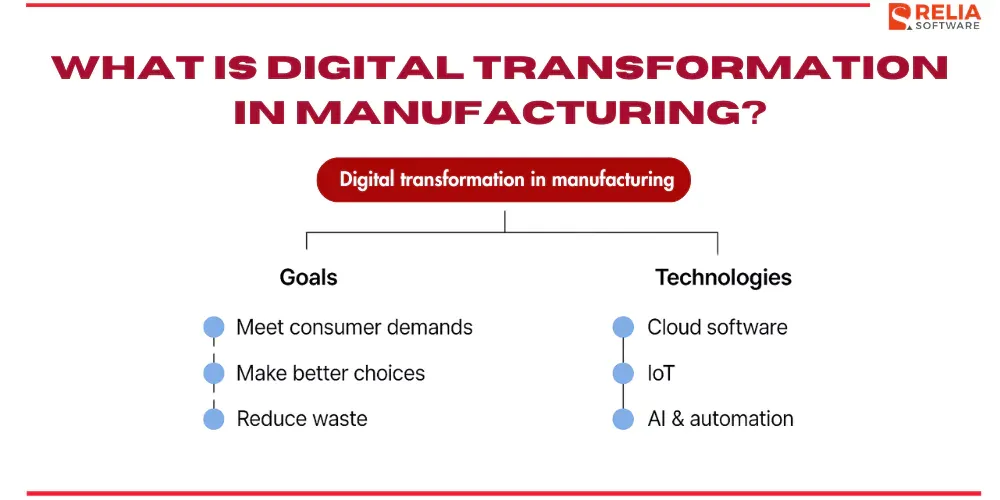
Historical Context
Manufacturing has always adapted to the times. The first industrial revolution brought steam engines and simple machinery at the beginning, during the late 1700s. This made hand production far more speedy. Later, electricity and manufacturing lines made it possible to make a lot of things at once. Then, computers and automation came into play, letting manufacturers run with more accuracy and less human involvement.
Now, we're in a new stage that many people call "Industry 4.0." This is when machines are all linked, data is everywhere, and digital systems make decisions faster. Companies today employ digital technologies to understand what's happening in real time, create better plans, and keep developing instead of only depending on robots to complete the tasks.
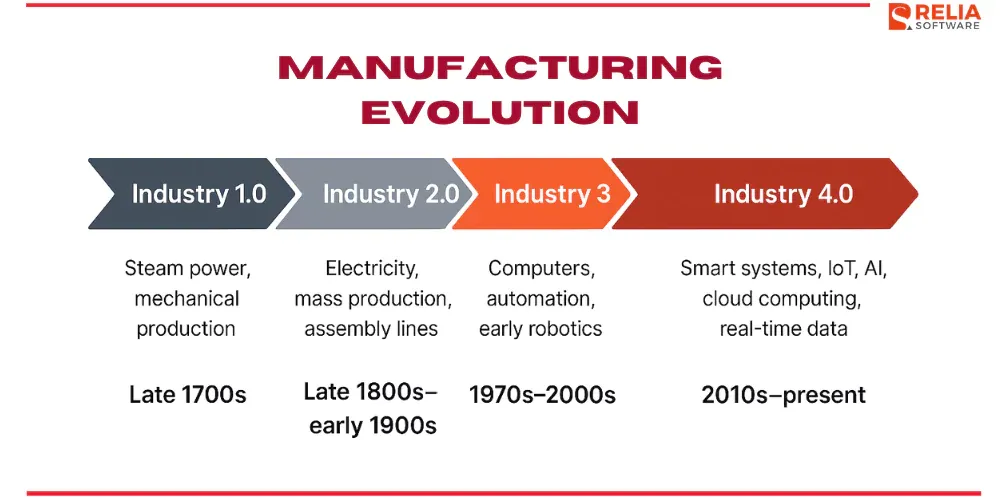
Why We Need Digital Transformation in Manufacturing?
Digital transformation doesn’t happen by accident. Manufacturers today are dealing with a set of clear, strong demands. These aren’t just trends but daily pressures that affect how businesses operate.
- Customization is expected: Buyers want more personalized products, whether it’s size, color, features, or packaging. This pushes manufacturers to be more flexible and responsive.
- Faster time-to-market matters: New ideas need to turn into products quickly. Delays give competitors a chance to move ahead. Companies need tools to speed up everything from design to delivery.
- Sustainability is no longer optional: Governments are adding new regulations. Customers are asking for greener choices. Manufacturers need to use resources wisely and reduce waste.
- Global competition never slows down: With global supply chains and digital access, companies aren’t just competing with their neighbors — they’re competing with firms around the world. That means every advantage counts.
These forces are strong enough on their own. But when combined, they create a clear message: change is not a choice. It’s a must.
Benefits of Digital Transformation in Manufacturing
Now, let's explore specifically how important digital transformation is in the manufacturing industry by getting to know its benefits side by side with the real problem it solves.
The Problem | How Digital Transformation Helps |
Machines fail without warning, causing long delays | Predictive maintenance tools warn teams early, so they can fix problems in advance |
Too much time is wasted tracking materials manually | IoT sensors and software track inventory in real time |
Production errors lead to wasted materials and money | AI systems catch mistakes early and suggest adjustments |
Employees have to wait for data or guess what’s wrong | Cloud dashboards give live updates from anywhere |
New products take too long to develop or adjust | Digital twins and 3D printing speed up testing and prototyping |
Teams work in silos, causing miscommunication | Digital platforms help share updates instantly between departments |
Customers expect faster delivery but systems are slow | Automation and better planning tools speed up order handling and shipping |
What Are The Key Technologies That Enable Digital Transformation in Manufacturing?
Artificial Intelligence (AI) & Machine Learning
AI helps machines and systems think like humans but faster and with larger data. In manufacturing, it’s mostly used to find patterns in huge amounts of information.
How it’s used:
- Detecting quality issues during production by scanning parts in real time
- Predicting machine failures based on vibration, temperature, and other signals
- Optimizing production schedules by learning from past delays
Internet of Things (IoT)
In factories, IoT means putting sensors on machines or equipment. These sensors send updates all the time, so workers don’t have to check things manually. The data shows what’s happening in real time, helping managers spot issues early without needing to be there.
How it’s used:
- Monitoring temperature, speed, or pressure inside machines
- Tracking materials as they move through each stage of production
- Alerting maintenance teams before equipment breaks down
>> Read more: 10 Best IoT App Development Companies in Vietnam
Digital Twins
A digital twin is a live, digital copy of a physical item — like a machine, a production line, or even a whole factory. It’s made using data from sensors, machines, and software. Because digital twins match the real system exactly, teams can test ideas, try changes, and spot problems without stopping actual production. It’s like having a safe, digital test area that runs alongside your factory.
How it’s used:
- Testing changes to a machine without stopping real production
- Running “what-if” scenarios to improve performance
- Helping engineers understand where delays or wear-and-tear may happen
Cloud Computing
Factories produce massive amounts of data from machines, workers, suppliers, and more. Cloud computing helps store this information safely online so teams can access it from anywhere.
How it’s used:
- Sharing production data between factory floors and headquarters
- Connecting design and manufacturing teams in different cities or countries
- Backing up systems in case something crashes on site
>> Read more:
- Top 10 Cloud Computing Programming Languages for Developers
- Top 10 Best Cloud Computing Platforms For Businesses
Additive Manufacturing (3D Printing)
3D printing builds objects layer by layer instead of cutting material away like in traditional manufacturing. It allows for shapes and designs that aren’t possible with standard tools. It’s especially useful when time is short or only a few parts are needed. Instead of waiting for suppliers, parts can be printed in-house, reducing the cost significantly.
How it’s used:
- Making quick, low-cost prototypes during product development
- Producing spare parts or tools on demand
- Customizing parts without building new molds or systems
Augmented Reality (AR) & Virtual Reality (VR)
AR shows digital information on top of the real world, usually through smart glasses or tablets. VR creates a full digital environment where users can train or test without physical risks. These tools reduce mistakes, improve safety, and cut down on training time — especially for complex tasks that are hard to explain with paper manuals.
How it’s used:
- Helping technicians see repair instructions overlaid on the real machine
- Letting designers walk through a factory layout before anything is built
- Training workers in a safe, digital version of the actual work environment
5 Practical Steps for Implementation Strategies
Starting digital transformation in manufacturing can feel like a big task, but it doesn't have to be complicated. Below is a practical roadmap that breaks the process down into five stages. Each one builds on the last, helping manufacturers go from where they are now to where they want to be.
Step 1: Know Where You Stand
Before doing anything new, it's important to understand your current setup. What systems are already digital? Which parts of the process still rely on paper or manual work? Are your machines connected? Can your teams access real-time data?
This stage often involves:
- Walking through the full production process
- Talking to staff at every level
- Listing out current tools and what they’re used for
- Spotting slow or error-prone areas
This isn’t about fixing anything yet — it’s about building a full picture of what’s going on so you can see where the biggest gaps or pain points are. The more honest and complete your assessment is, the better your plan will be.
Step 2: Set Clear Goals
Once you know what’s working and what’s not, you can start planning. This step is about setting priorities and breaking the transformation into small, clear steps.
Ask questions like:
- What problem should we solve first?
- What’s the most important goal — faster output, lower waste, better visibility?
- What’s our budget and timeline?
Create a short- and long-term plan. The short-term covers quick wins. The long-term guides bigger upgrades like cloud systems or full automation. Don’t try to do everything in one go. Spreading out your plan makes it easier for your team to adjust and gives time to learn what works best. Digital transformation isn’t a fixed path — it changes as your business grows.
Step 3: Technology Selection
Now comes the part where you select the tools and systems that will support your goals. This step is often the most overwhelming. Remember that there’s no one-size-fits-all solution. The best technology for your business depends on your goals, team skills, and existing systems.
Start by matching your main problems with available solutions:
- If machines break down too often, use predictive maintenance systems with sensors.
- If there’s poor communication between teams, consider cloud platforms for real-time updates.
- If product designs need to change frequently, you may have to use digital twins or 3D modeling tools.
- If you want faster prototypes, additive manufacturing, like 3D printing, can help.
Focus on tools that are easy to integrate and can grow over time. Avoid systems that lock you into one vendor or require a full system rebuild just to get started. Also, think about how easy it is to train your team to use them.
Step 4: Prepare Your Team
Technology alone won’t fix anything. People have to use it well. That’s why this step is about helping teams learn, adjust, and see the value in the new system. The biggest reason digital transformation fails isn’t because of the technology — it’s because people aren’t ready for the change.
To avoid that:
- Explain clearly why changes are happening and how they help your workers.
- Encourage workers to share their thoughts, questions, or concerns.
- Start with small rollouts so people don’t feel overwhelmed.
- Provide simple training that focuses on real tasks, not technical theory.
- Show success stories, even small ones, to build trust in the new system.
Some workers may worry that automation means job cuts. Reassure them. In many cases, digital tools help workers do their jobs better, not replace them. When the team feels involved and supported, they’re much more likely to use the new tools correctly and even suggest ways to improve things further.
Step 5: Continuous Improvement
Digital transformation is never “done.” After tools are in place and people are trained, the next step is to keep checking what works and what doesn’t.
That’s why the final step is to review your results often and keep looking for small wins. Do regular check-ins:
- What data are we collecting? Is it helping decision-making?
- Are there fewer errors or breakdowns?
- Can we automate any other tasks?
- Is the team comfortable using the tools?
Review results, learn from them, and adjust. Over time, these improvements add up and become part of the company’s everyday rhythm.
Challenges and Solutions
Challenge 1: Resistance to Change
One of the biggest challenges in going digital is that many people feel nervous about it. Some factory workers may worry that new tools will take their jobs away. Others might feel confused, overwhelmed, or simply unsure if the change is really needed.
This doesn’t mean workers have bad attitudes. Most of the time, it’s just fear of the unknown or not having enough information. If people don’t understand how new tools will help them, or if they’re not part of the process, they may resist or avoid using the tools at all.
Solutions:
- Explain clearly why the change is happening and how it will help make their jobs easier
- Let workers try the new tools early and give feedback — this helps them feel involved
- Keep training simple and focus on what they need for their specific role
- Celebrate progress — when people see that the tools actually help, they’re more likely to support the change
Challenge 2: Cybersecurity Concerns
Digital tools can make factories work better, but they also bring new risks. When machines, systems, and data are connected, especially over the internet or cloud, they can be targets for cyberattacks. This could mean things like hacked systems, stolen data, or someone taking control of important equipment.
Solutions:
- Use secure networks and regularly update passwords and software.
- Set clear access rules — only the right people should reach certain data.
- Work with IT experts to spot weak points and fix them early.
- Back up your data often and test your recovery plan.
>> Read more: In-depth Guide To Cybersecurity in Software Development
Challenge 3: Integration with Legacy Systems
Many factories still use old machines and software that have been around for years or even decades. These systems were built before modern tools like cloud software or IoT devices existed, so they often don’t work well with newer technology.
Trying to add digital tools on top of these older systems can be tough. Replacing everything at once isn’t realistic. It’s expensive and could stop production. That’s why connecting old and new systems is one of the most common and difficult parts of going digital.
Solutions:
- Use digital tools that are made to work with older equipment — many platforms now support slow upgrades.
- Add connectors or small programs (called middleware) that help old and new systems share data.
- Start small. For example, try connecting machines in just one area before expanding to the whole factory.
Challenge 4: Skill Gaps
Digital tools can be really helpful, but they only work if people know how to use them. If workers don’t fully understand how the tools work, they might avoid using them and make mistakes. This can lead to slowdowns or confusion on the job.
Solutions:
- Provide simple, hands-on training — focus on showing, not telling.
- Pair experienced workers with tech-savvy staff for on-the-job support.
- Offer regular refresh sessions as tools evolve.
- Bring in outside help temporarily if you need to train teams quickly.
Future Trends in Manufacturing Digital Transformation
Emerging Trends - Industry 5.0 and human-centric manufacturing
The next big step of digital transformation in manufacturing is called Industry 5.0. Instead of focusing only on machines, it puts people back at the center. Workers will use smart tools to make their jobs easier, while robots handle repetitive tasks. It’s not just about working faster — it’s about working smarter, with people and machines helping each other.
Sustainability
More factories are trying to be more eco-friendly. They’re using digital tools to track how much energy, water, and materials they use and then finding ways to cut down on waste. Many firms are also adding solar panels or other clean energy sources. Products are now being designed to be easier to repair, reuse, or recycle. In the future, being green won’t be a choice; it will be something customers and governments expect.
Global Impact
Digital tools are helping smaller companies grow quickly and compete with bigger brands. Cloud software and online tracking are now easier and more affordable to use. Because of this, factories don’t have to be in just one place. Companies can now build smaller, smarter factories closer to their customers to speed up delivery and respond faster to local needs.
Transform Your Factory with Relia Software
Relia Software provides end-to-end digital transformation services to help manufacturers modernize their processes and compete in a fast-changing industry. We bring deep expertise in AI, IoT, big data analytics, cloud migration, microservices, and enterprise mobility — all key technologies for building smart, efficient factories.
Our AI/ML services use predictive analytics and smart automation to automate tasks. With IoT integration, we can help factories monitor machines in real time, making maintenance faster. The cloud-native solutions also improve access to information and help reduce waste while boosting product quality.
Relia Software doesn’t just build tech normally, we always make sure the outcome fits your factory’s real needs. With a history of turning complex challenges into practical, working solutions, we can be a trusted partner for manufacturers ready to take the next step into industry 4.0 manufacturing.
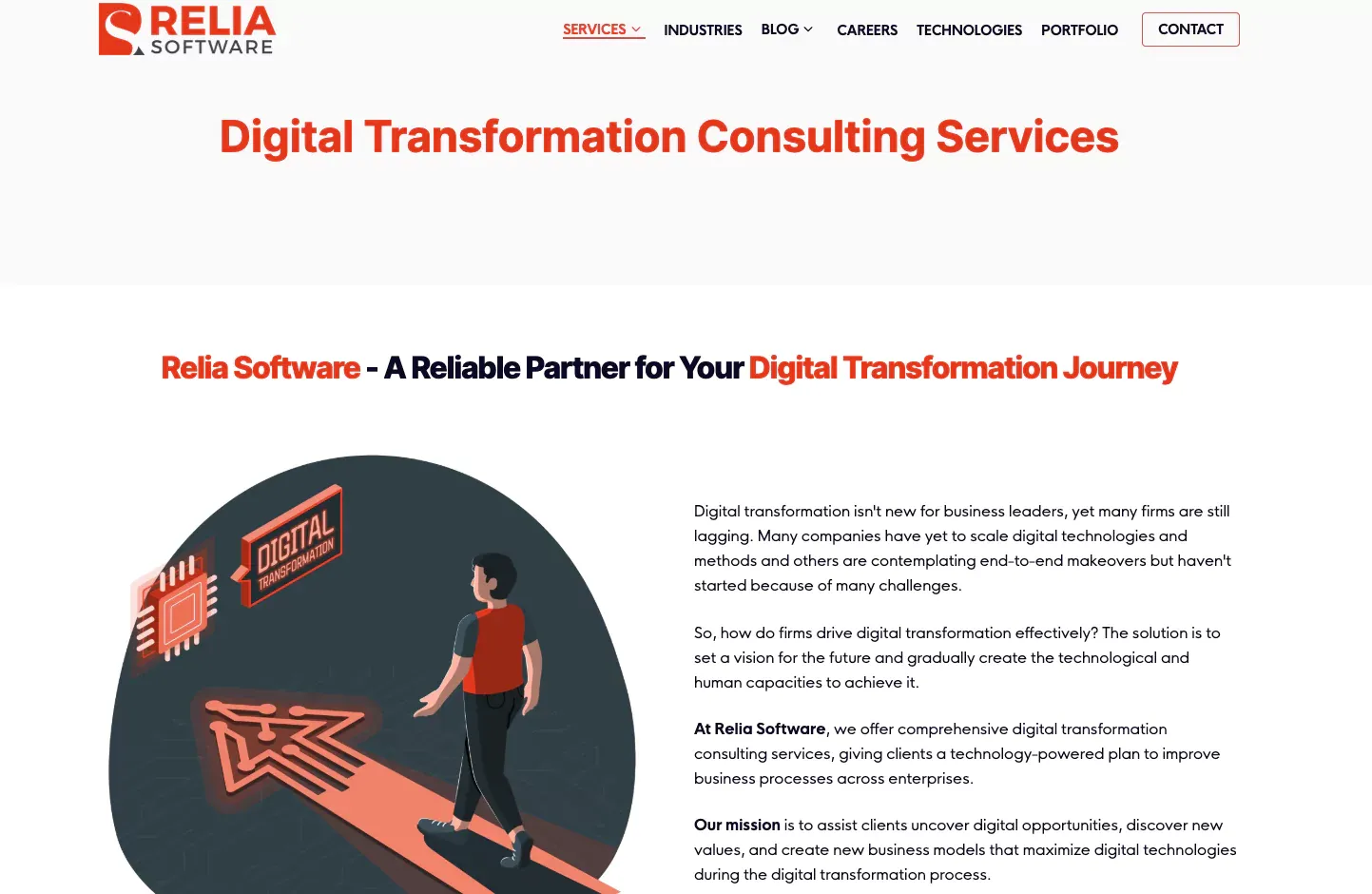
Conclusion
Digital transformation in manufacturing is changing how manufacturers work, from daily operations to long-term planning. It’s no longer just about using machines or software. It’s about making smarter decisions, reducing waste, improving quality, and helping people do their jobs better with the right tools. Whether you’re upgrading an old system or starting fresh, taking small steps with clear goals can make a big difference.
The journey takes time, but it’s worth it. With the right approach, digital transformation can help manufacturers work faster, respond to change, and build a stronger business for the years ahead.
>>> Follow and Contact Relia Software for more information!
- automation